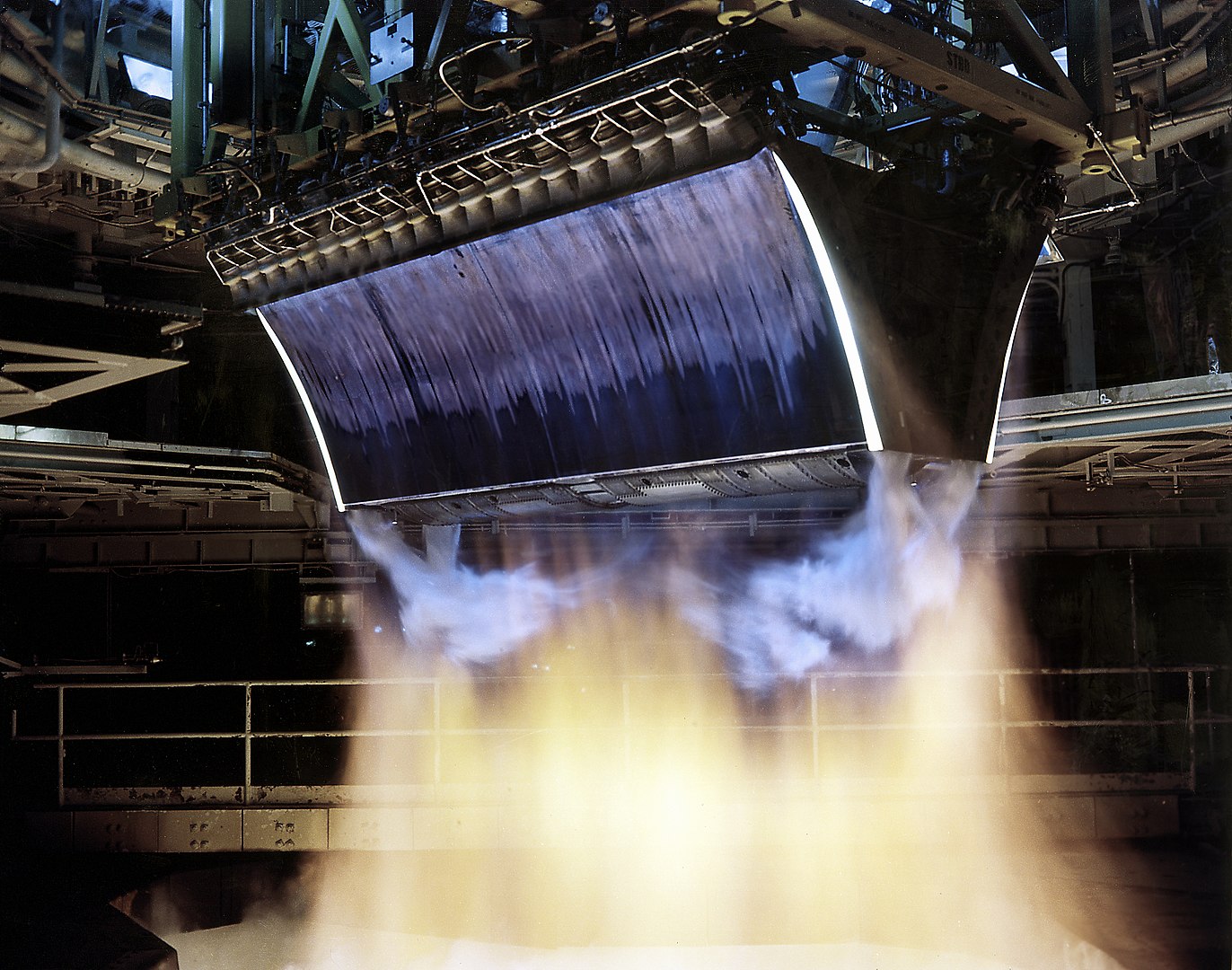
POLARIS Raumflugzeuge tasked with Linear Aerospike engine study
Published on Thu, 27.04.2023 – 16:46 CEST in R&D, covering POLARIS RaumflugzeugeAerospike engines are regarded as a kind of holy grail in space travel. Researchers have been working on the implementation of this promising propulsion principle since the 1950s. Although only prototypes exist so far, new materials and the possibilities of additive manufacturing could be the decisive gamechangers. The Bremen-based startup POLARIS Raumflugzeuge has now been commissioned to conduct a study on the development and flight testing of a Linear Aerospike rocket engine.
Lighter, smaller, more fuel-efficient - in theory, aerospike engines outstrip conventional rocket engines. In practice, however, there are a number of hurdles to overcome before they can be used. Unlike conventional rocket engines, an aerospike engine does not have a conventional nozzle at the rear end of the engine. Instead, it has a nozzle structure that extends around the circumference of the engine and starts at the base of the engine. This makes it possible to continuously adjust both thrust and efficiency over a wide range of speeds and altitudes. A major drawback, however, is the temperatures generated in the process, which are extremely stressful on the materials used. This can be remedied by a large number of cooling ducts, but this further increases the complexity of this type of engine.
Additive manufacturing and artificial intelligence make aerospike engines tangible
This is where the Fraunhofer Institute for Material and Beam Technology IWS and the Institute of Aerospace Engineering (ILR) at TU Dresden came in. In 2019, they were able to present an aerospike engine with 500 newtons of thrust that was additively manufactured. Colloquially referred to as 3D printing, this involves a laser melting a nickel-based superalloy in the metal powder bed to create the components layer by layer. On the test stand, however, the Fraunhofer IWS and ILR prototype still showed problems with the cooling system and fuel injection. An improved successor should then already have a thrust of 6,000 N. The AeroSPIke Rocket Engine Realisation (ASPIRER) project has also been funded by the European Space Agency ESA since 2020.
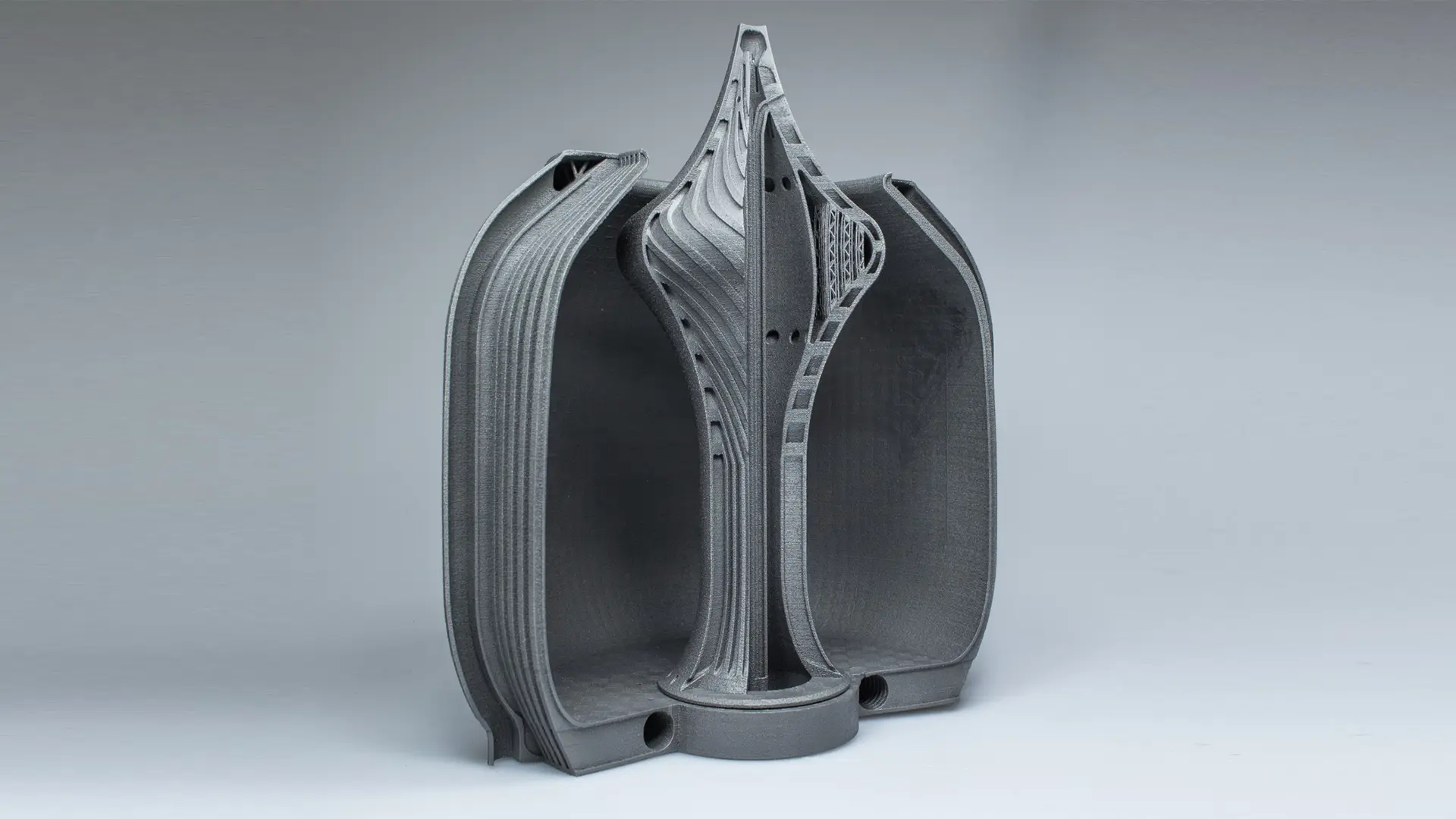
© Fraunhofer IWS
In August 2022, Hyperganic announced it had manufactured the world's largest 3D-printed aerospike engine. But instead of focusing on a specific design, the Munich-based company developed a series of algorithms to describe the construction of such an engine. As a result, hundreds of feasible variants were developed, some of which were selected for printing. One, according to the company, is the most complex 3D-printed object to date and the first algorithmically designed rocket engine in existence.
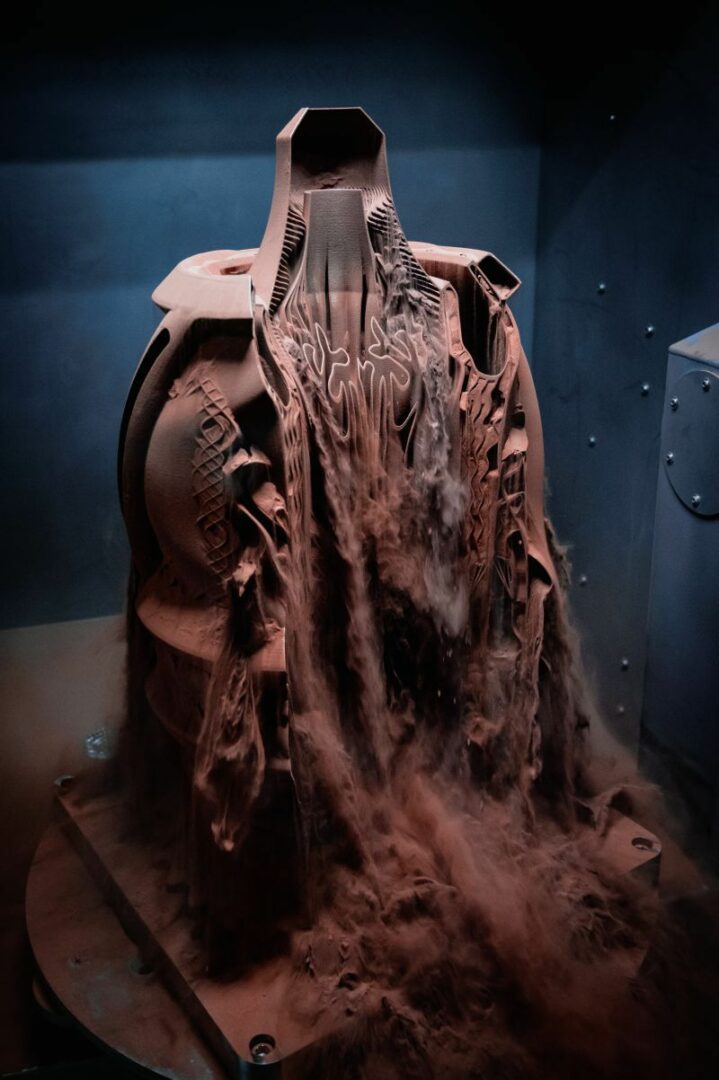
© AMCM / Hyperganic
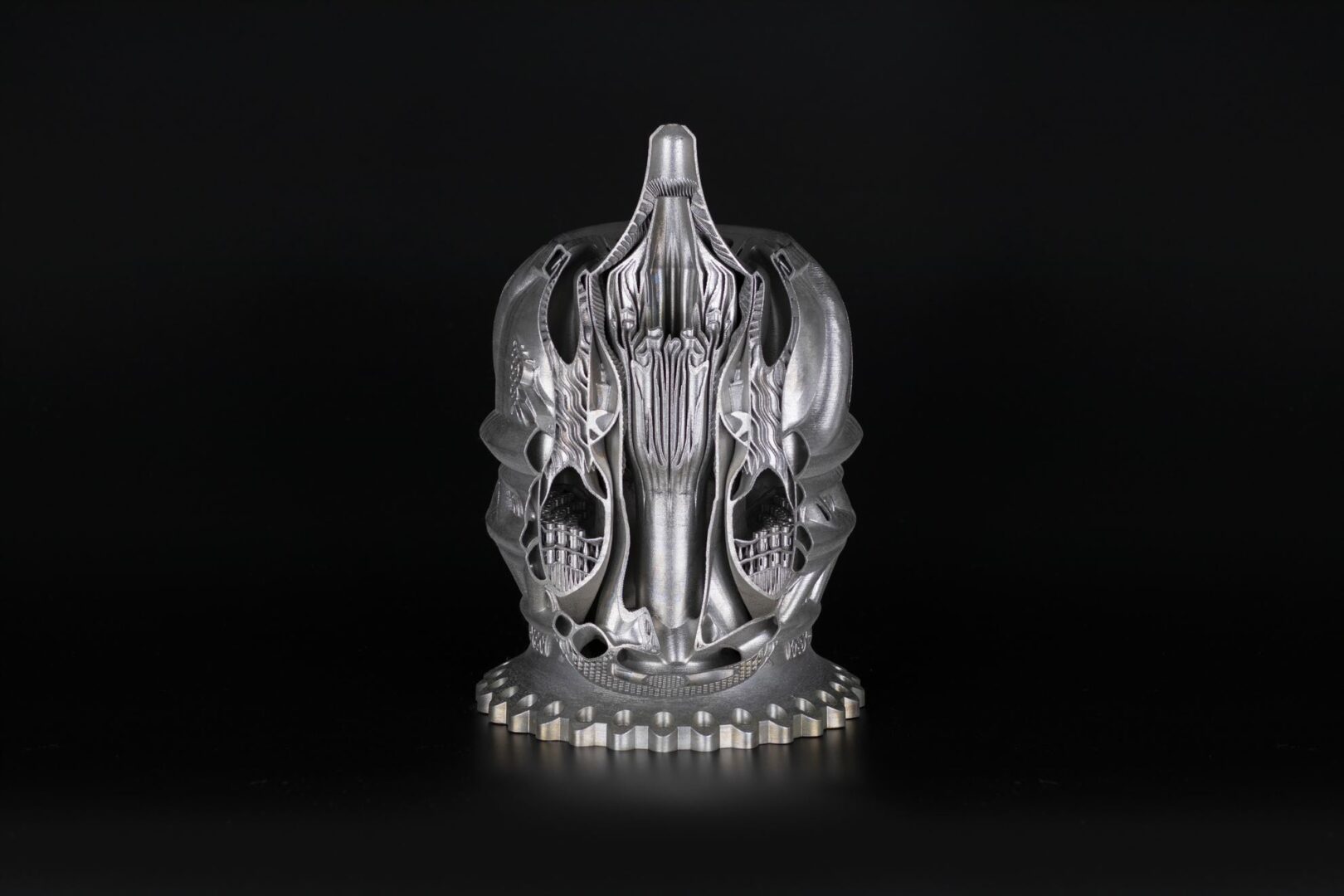
© EOS / Hyperganic
POLARIS Raumflugzeuge relies on Linear Aerospike (LAS) rocket engines
While research is currently focusing on the realization of a cylindrical engine, POLARIS Raumflugzeuge is relying on linear aerospikes (LAS). These were already to be used as the main propulsion system on the planned Space Shuttle successor X-33/VentureStar. Ground tests already took place in the 1990s. A LAS cold-stream demonstrator was also installed and flown on the back of an SR-71 Blackbird. However, they have never been used in regular flight operations until now. But that could happen now.
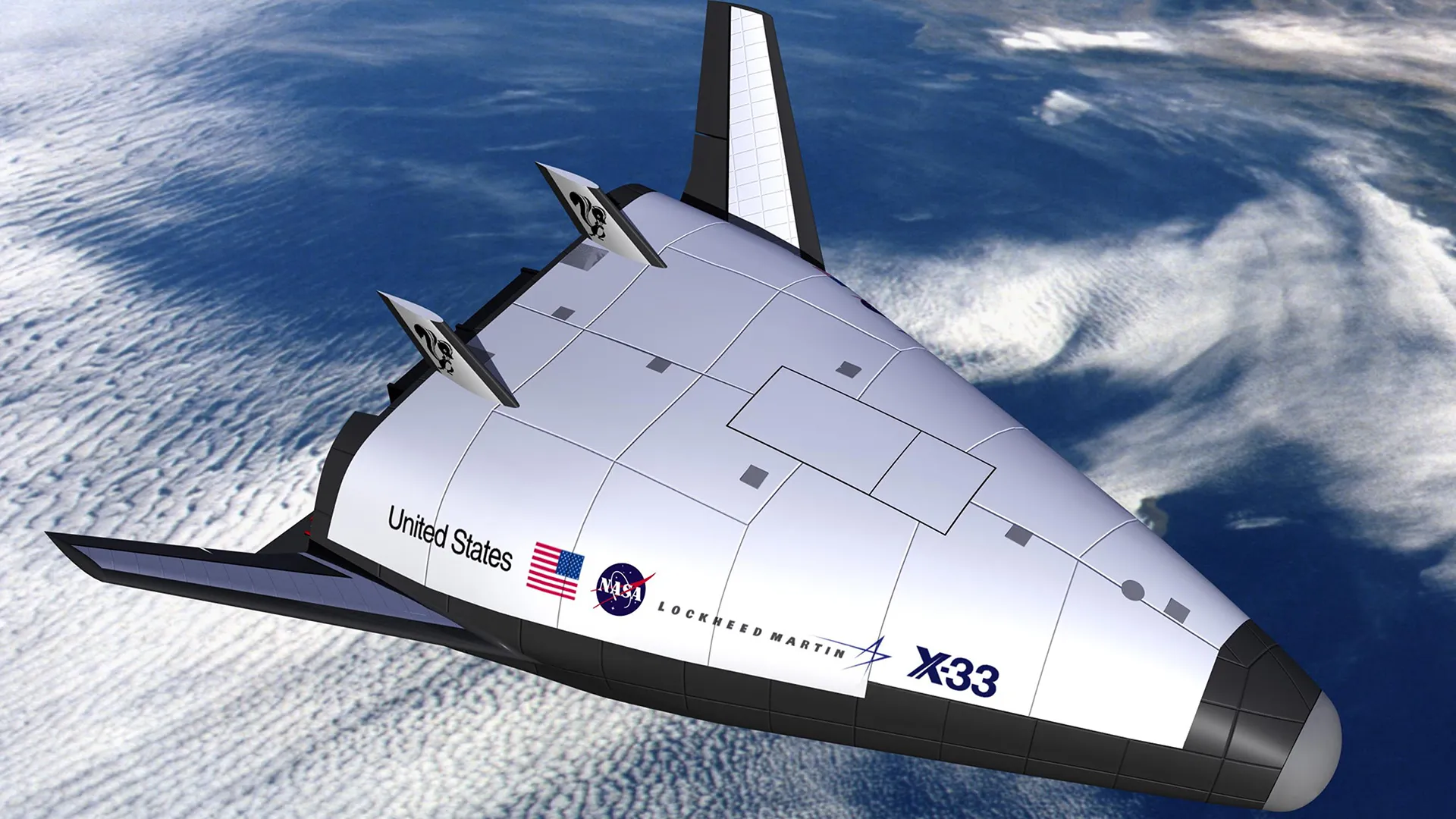

Denn aufgrund ihrer Geometrie sind LAS für das vom Bremer Startup POLARIS geplante, besonders flache Raumflugzeug besonders interessant. Wie das Unternehmen um Alexander Kopp mitteilt, seien LAS einfacher zu integrieren und hätten einen geringeren Luftwiderstand während des turbinengetriebenen Reisefluges oder des Gleitfluges beim Wiedereintritt. Zudem könne damit das Problem möglicher Tail-Strikes – das ungewünschte Berühren der Startbahn durch das Flugzeugheck – bei Start und Landung gelöst werden. Insofern ist es nur konsequent, dass POLARIS LAS-Raketenantriebe als Basisantriebssystem ausgewählt hat.
German armed forces commission POLARIS Raumflugzeuge with study
First, and foremost, this type of engine has to be qualified. To this end, the German Federal Office of Bundeswehr Equipment, Information Technology and In-Service Support (BAAINBw) has commissioned POLARIS to study the potential of a LAS as a propulsion element in a spacecraft demonstrator. With this new contract, POLARIS has already been awarded the third study contract in succession by the German Armed Forces in the field of spacecraft with increasing complexity. For the aerospike flight validation, POLARIS will build another full-scale spacecraft demonstrator. Compared to its three predecessors already built and flown, this one will be even larger and heavier. As part of the study, a LAS rocket engine will then also be fired and tested in flight for the first time.
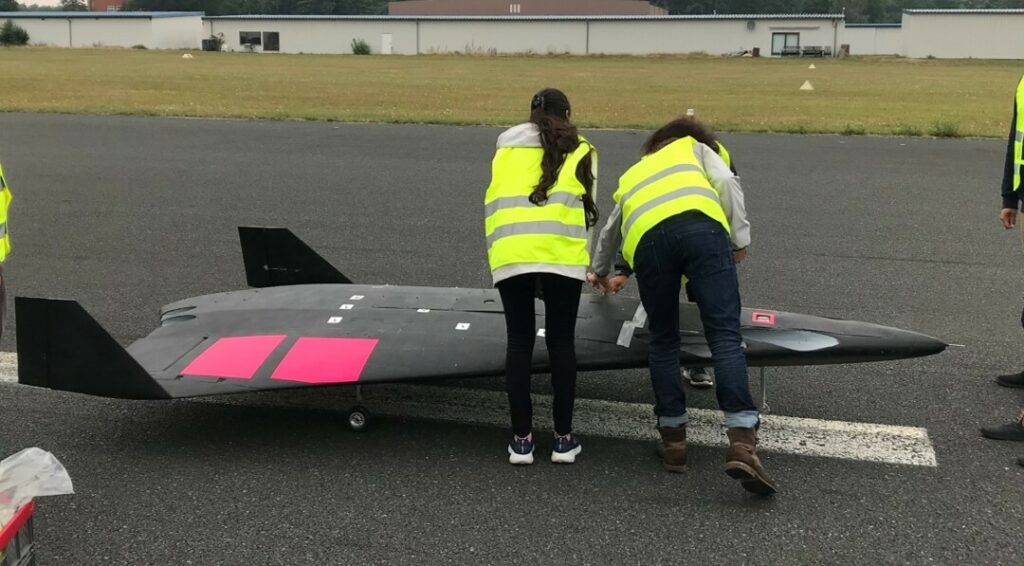
© POLARIS Raumflugzeuge

© POLARIS Raumflugzeuge

© POLARIS Raumflugzeuge
Whether the hopes and expectations will be fulfilled remains to be seen. But it is already clear that the flight validation is an important milestone on the way to an operational spaceplane. Since it is not possible to launch conventional rockets from Germany, a space plane has enormous potential to make a decisive contribution to sovereign access to space.